Ergonomists, Not Economists on Improving Business
The Start of Occupational Safety and Ergonomics
In the 1930s while San Francisco’s Golden Gate Bridge was under construction, nineteen workers fell from the structure’s mind-boggling heights in different incidents over the years and lived to form a group called the ‘Half Way to Hell Club.’ They owed their lives to a heavy rope mesh net under the bridge that cost chief project engineer Joseph Strauss a significant sum of money. At that time, no laws existed that required this safety measure.
The relationship between a worker and the workplace has been a process of improvement and its consideration is a relatively recent societal development. This process has led to the emergence of ergonomics in the work environment designing or arranging workplaces, products and systems so that they fit the people who use them.
A Rapid Shift Toward Improvement
Occupational safety and health as we know it today came from the rapid rise in standards and expectations for well-being through the industrial revolution. As recent as the construction of the Golden Gate Bridge, a safety net protecting workers from falling to their deaths was a generous condition for labor. Today, there is an industry for goods and services dedicated to safe and effective human interfacing and interaction with the workplace environment.
For example, Fremont, California’s Ergobility provides consulting services to offices and workspaces to help them evaluate products and practices to improve ergonomic standards and improve the overall employee experience. Given the increasing prioritization of these aspects of work culture, these kinds of services are likely to become more popular in the future.
In Cleveland, Ohio, Michael O'Donnell, vice president of operations at the Manufacturing Advocacy and Growth Network (MAGNET) has been helping the Ohio region's builders assess their ergonomic requirements. O’Donnell points to the pandemic and shifts in the American labor market as forces that have driven workplace ergonomics into greater prominence.
Brecksville-based Knight Ergonomic and Assembly works mostly in the automotive sector and caters to companies including Ford, GM, Honda, Toyota, and Nissan. Vice president Joel Haller explains that "the cost of having a worker not able to work is a driving factor. You also want to make your workplace more palatable so people will join your company.”
In contemporary advanced countries, most people work in environments that adhere to certain safety protocols such that work-related injury is a rare concern. Of course there are still jobs in advanced economies that can be physically dangerous and risky, but those too exist in a framework of minimizing hazards as much as possible. The overall trend in workplace safety has been toward greater degrees of worker-centric measures to improve safety, comfort, and efficiency. October was even designated National Ergonomics Month in 2003 by the Human Factors and Ergonomics Society (HFES).
Concepts in ergonomics have become staples in American workplaces. These include maintaining good posture, taking breaks and doing stretches, maintaining a fitting workstation with correct proportions on the keyboard and desk height, and using appropriate machinery for strenuous tasks among others. Improvements in technologies, methods, and standards of living have given rise to greater expectations for worker conditions. Hopefully, this trend will push toward better experiences for individuals in the workplace and improve relations across the labor market in the future.
The Local Economist
Your Home for Entrepreneurial News, Local Business Spotlights, and Trends that Matter
join the newsletter
Recent Posts
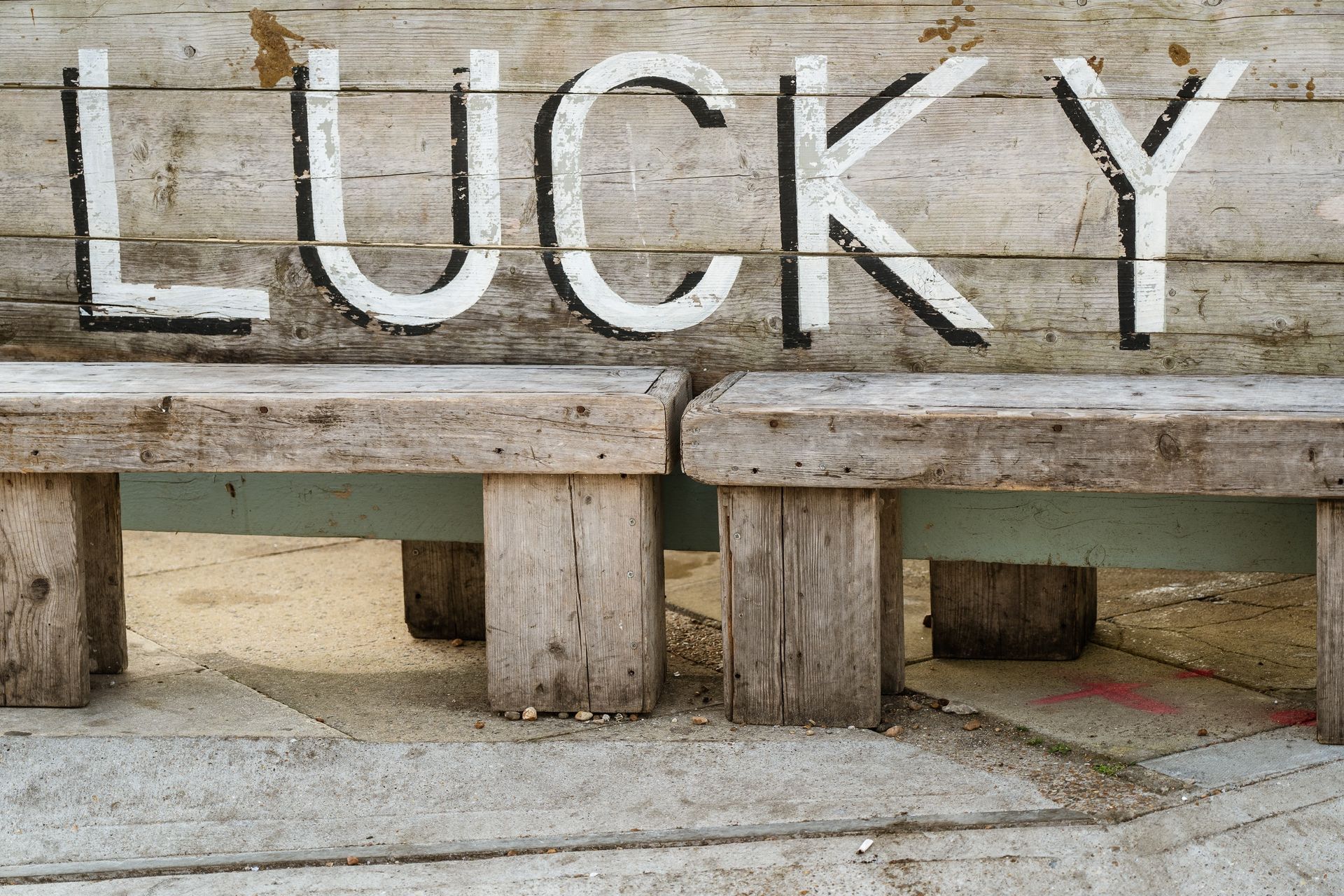
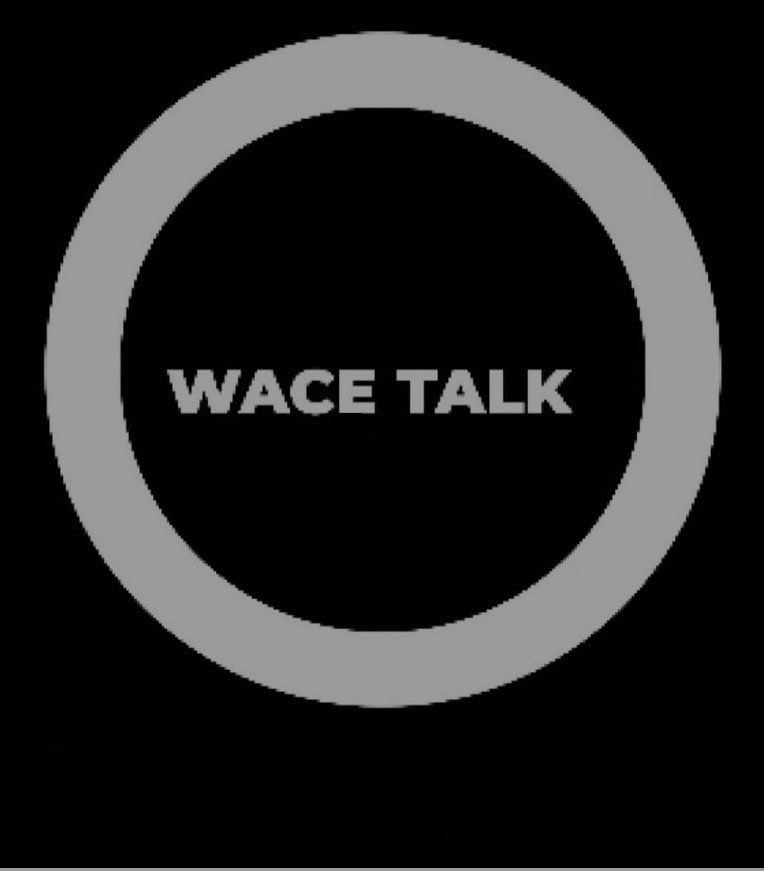
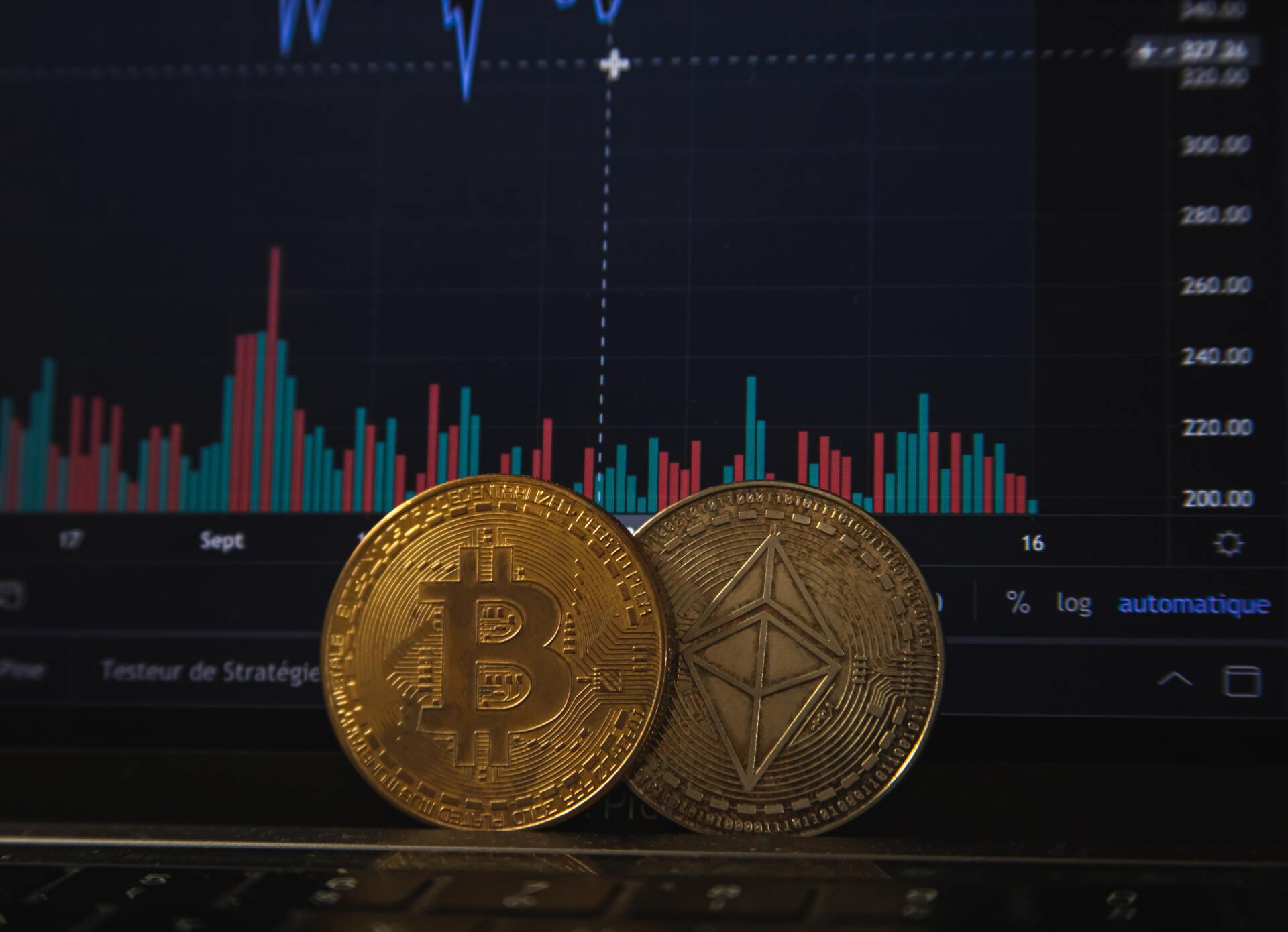
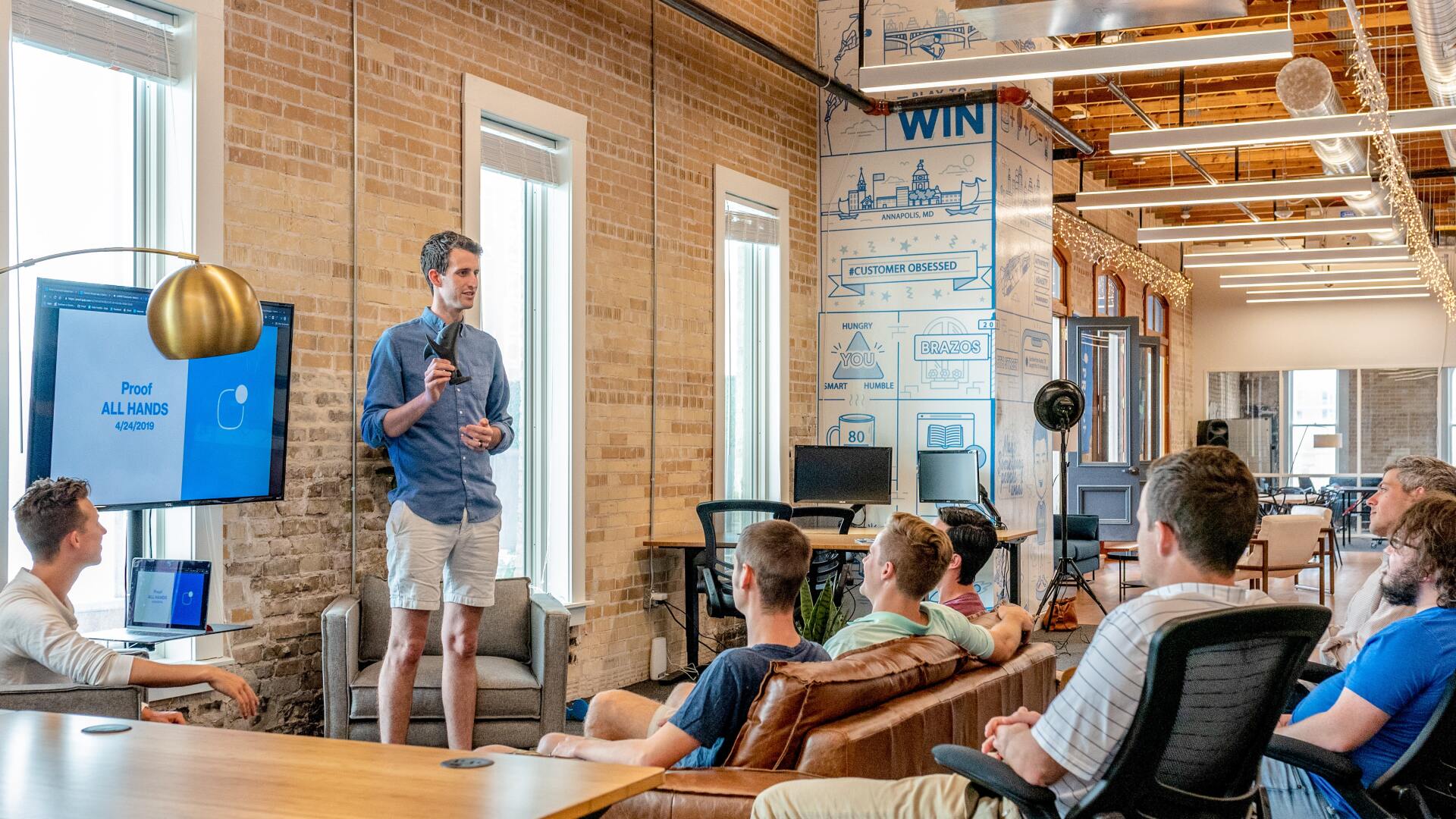
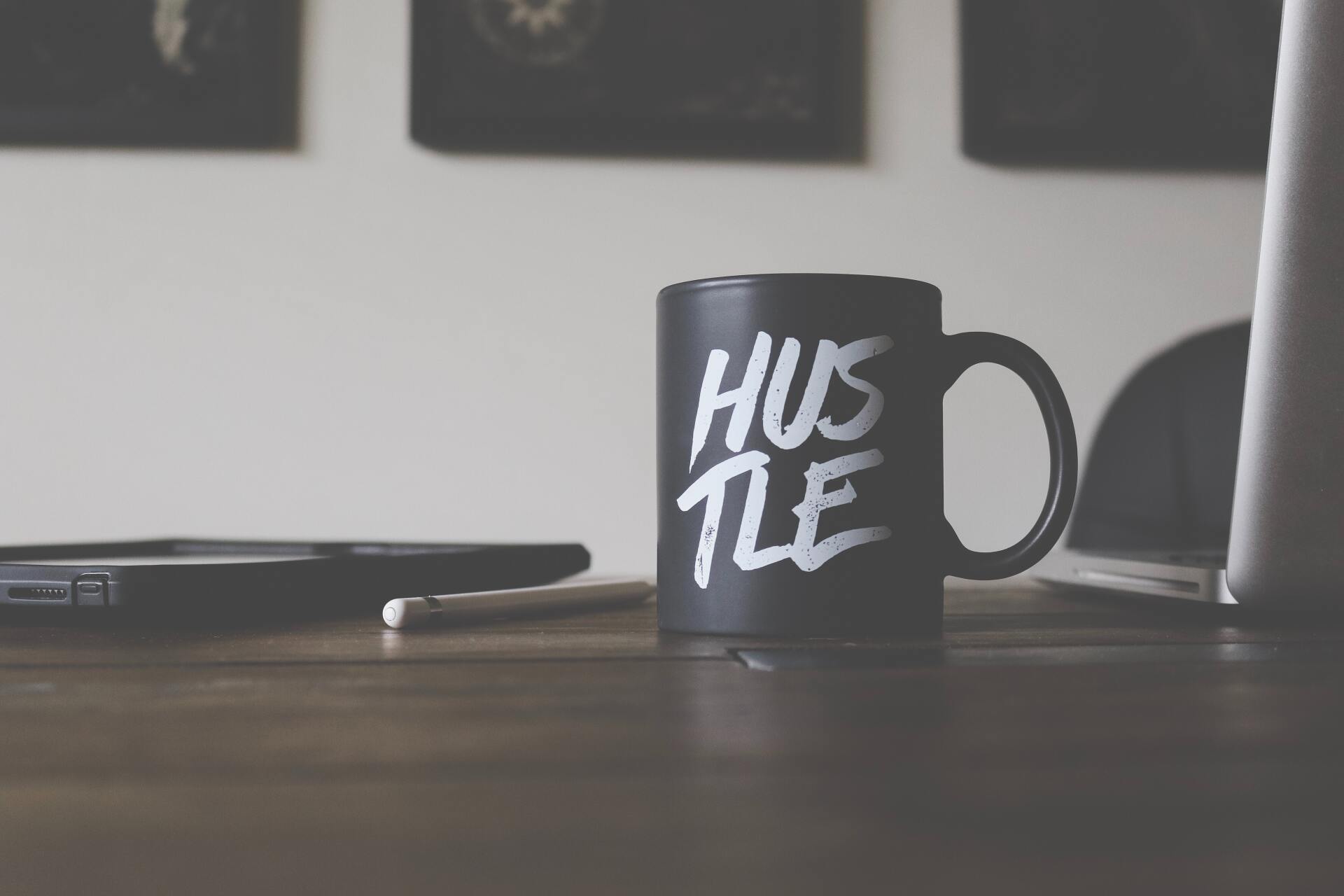
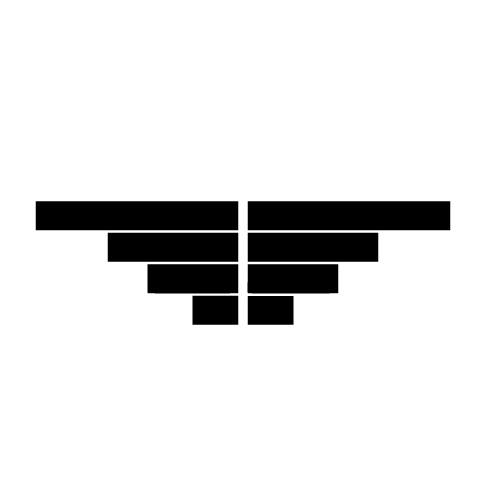
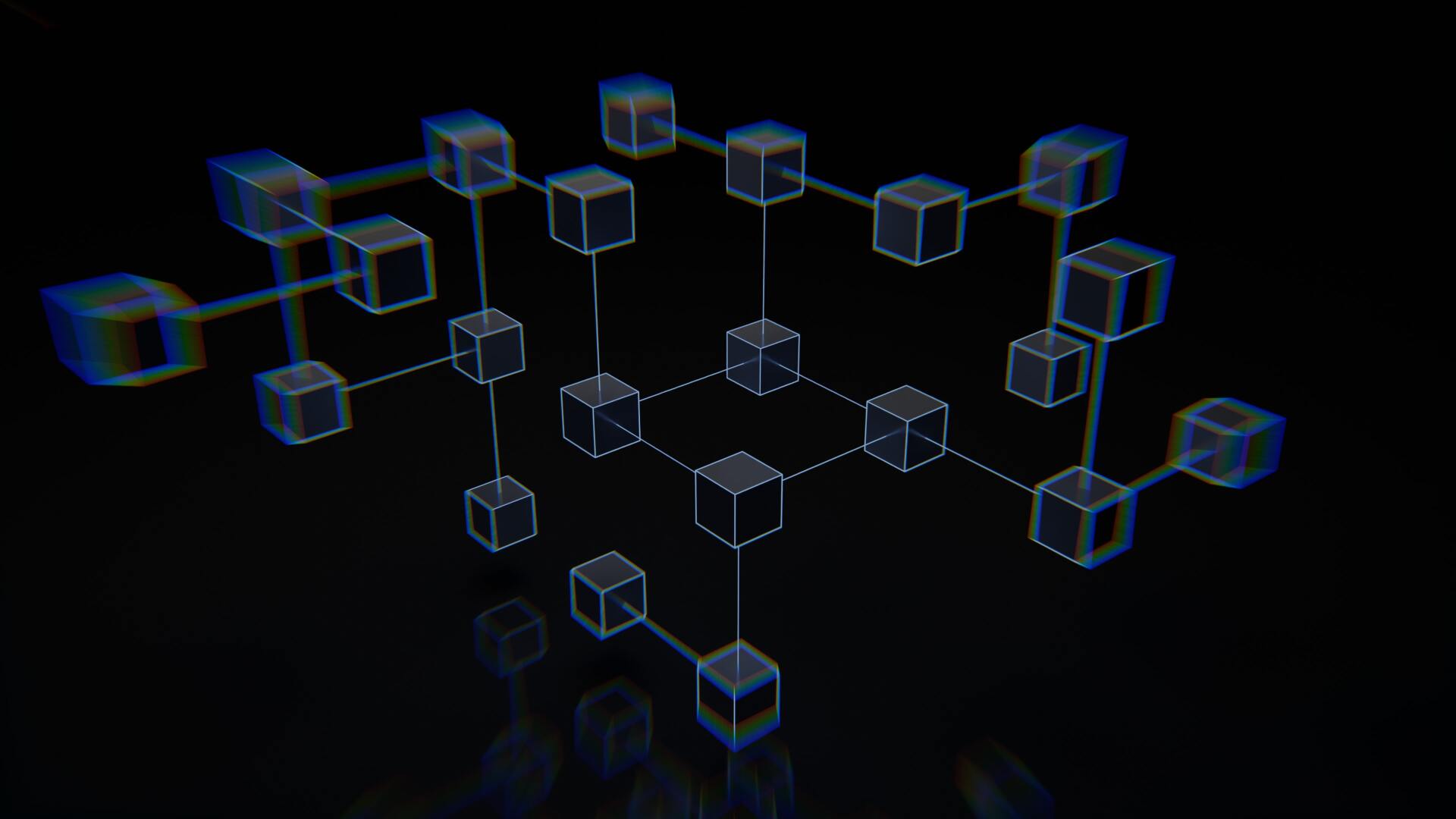
Share This...
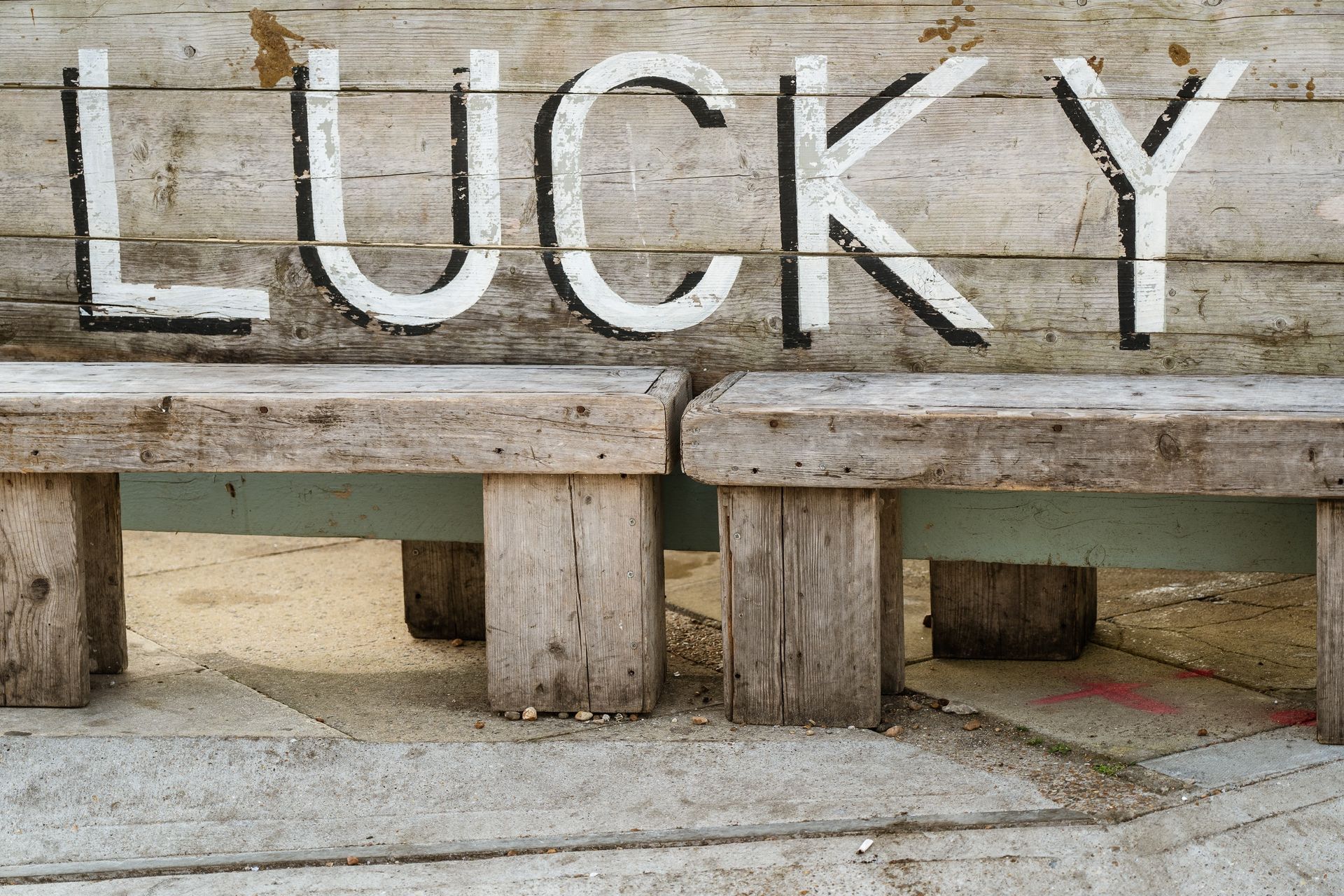
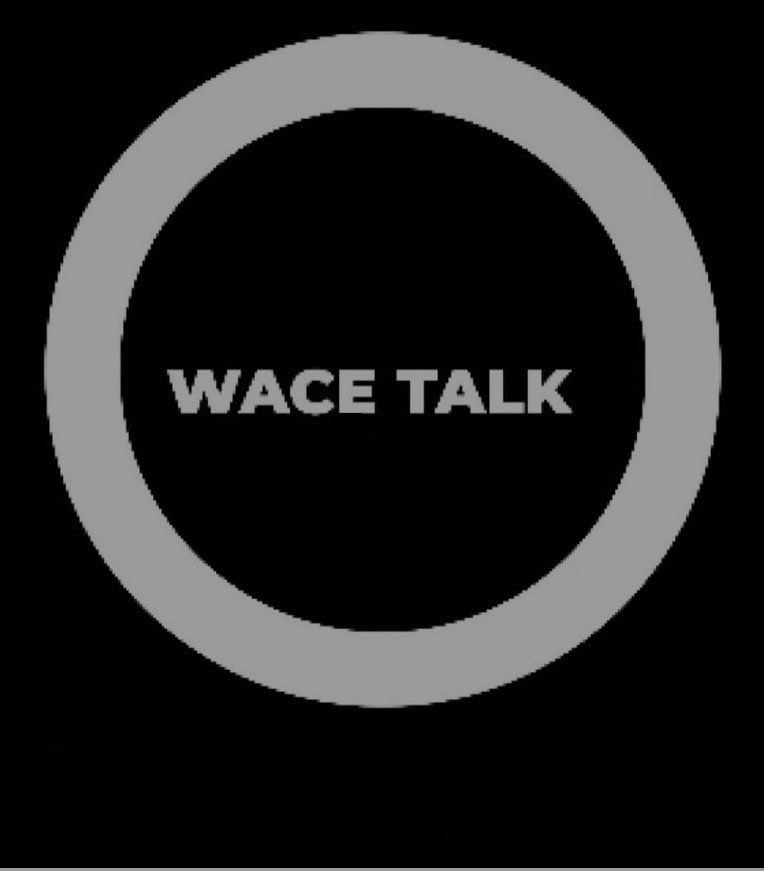
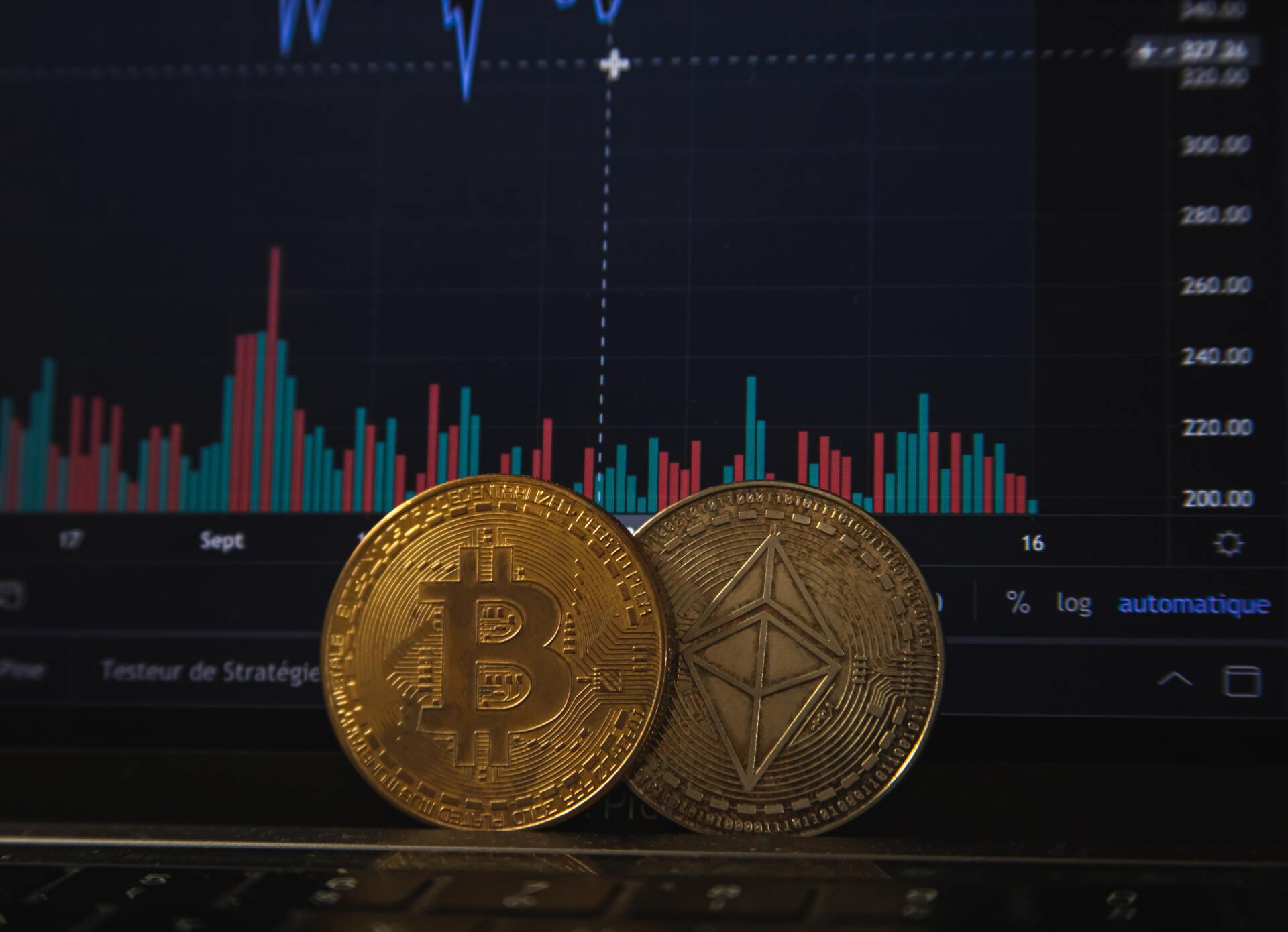